五大陶瓷基板材料特性及应用大全
浏览数量: 0 作者: 先进陶瓷材料 发布时间: 2022-09-07 来源: 先进陶瓷材料
["wechat","weibo","qzone","douban","email"]
近年来,电子器件工作电流大、温度高、频率高,为满足器件及电路工作的稳定性,对芯片载体提出了更高的要求。陶瓷基板具有优异的热性能、微波性能、力学性能以及可靠性高等优点,可广泛应用于这些领域。
陶瓷基板在消费市场上的应用越来越多,但国内陶瓷基板与国外相比还有很大的差距,部分基板原材料仍需要进口,例如高纯氮化铝粉体。 目前应用于陶瓷基板的陶瓷材料主要有:氧化铍(BeO)、氧化铝(Al2O3)、氮化铝(AlN)、氮化硅(Si3N4)和碳化硅(SiC)等。 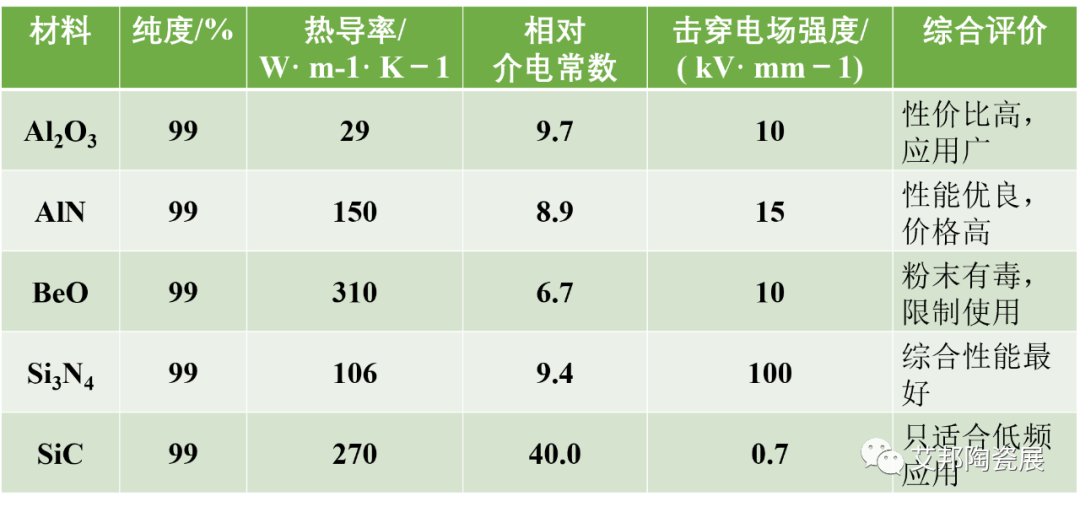
一、氧化铍(BeO)
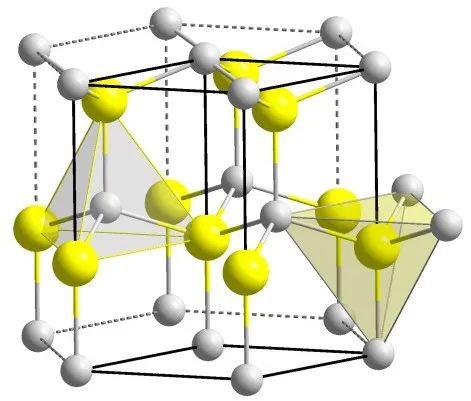
BeO为纤锌矿型结构,单胞为立方晶系。其热传导能力极高,BeO质量分数为99%的BeO陶瓷,室温下其热导率(热导系数)可达310W/(m·K),为同等纯度Al2O3陶瓷热导率的10倍左右。不但具有极高的传热能力,同时还具有较低的介电常数和介电损耗以及高的绝缘性能和机械性能等特点,在需要高导热的大功率器件及电路的应用中,BeO陶瓷是首选材料。 BeO的高热导率和低损耗特性迄今为止是其他陶瓷材料不可比拟的,但BeO有非常明显的缺点,其粉末有剧毒。
二、氧化铝(Al2O3)
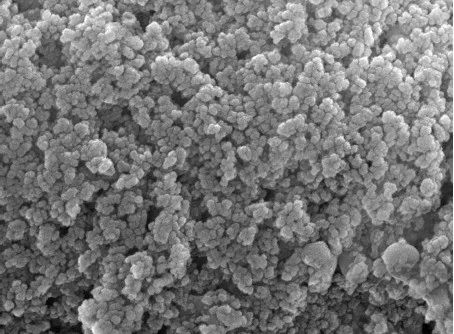
Al2O3的同质多晶体可达10多种,其主要晶型有如下4种:α-Al2O3、β-Al2O3、γ-Al2O3和ζ-Al2O3。其中α-Al2O3活性最低,是4种主要晶型形态中最稳定的一种,其单元晶胞是一个尖的菱面体,属于六方晶系。α-Al2O3结构紧密,为刚玉型结构,能稳定存在于所有温度下;当温度达到1000~1600℃时,其他变体都会不可逆地转变为α-Al2O3。 随着Al2O3质量分数的增加以及相应玻璃相质量分数的减少,Al2O3陶瓷热导率迅速上升,当Al2O3质量分数达到99%时,其热导率相较质量分数为90%时提高了一倍左右。 虽然增加Al2O3的质量分数可以提高陶瓷的综合性能,但是同时提高了陶瓷的烧结温度,间接导致了生产成本的增加。
三、氮化铝(AlN)
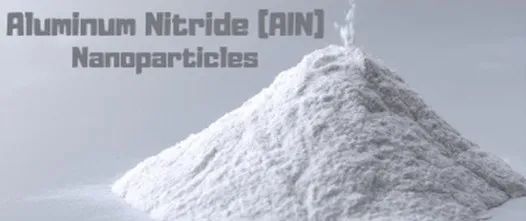
AlN是一种具有纤锌矿结构的Ⅲ-Ⅴ族化合物,其单元晶胞为AlN4四面体,属于六方晶系,具有很强的共价键,因而其机械性能优良、抗弯强度较高。理论上其晶体密度为3.2611g/cm3,因而具有高导热性能,纯净的AlN晶体室温热导率高达320W/(m·k),热压烧制的AlN基片热导率可达150W/(m·K),为Al2O3的5倍以上,热膨胀系数为3.8×10-6~4.4×10-6/℃,与Si、SiC和GaAs等半导体芯片材料热膨胀系数匹配良好。
AlN陶瓷比Al2O3陶瓷具有更高的热导率,在大功率电力电子等需要高热传导的器件中逐渐替代Al2O3陶瓷,应用前景广阔。AlN陶瓷还因其具有低的二次电子发射系数,被看作是功率真空电子器件输能窗口的首选材料。
四、氮化硅(Si3N4)
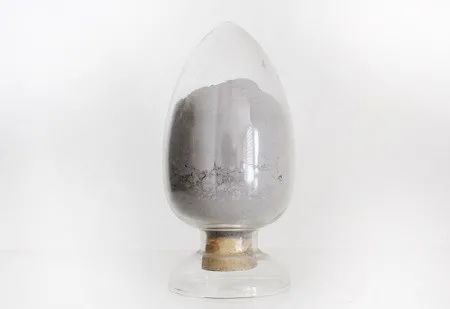
Si3N4为共价键化合物,有三种晶体结构:α-Si3N4、β-Si3N4和γ-Si3N4。其中α-Si3N4和β-Si3N4是最常见的晶型,为六方结构。单晶Si3N4热导率可达400W/(m·K),然而由于其为声子传热,实际晶格中存在空位、位错等晶格缺陷,且杂质造成声子散射变大,实际烧制的陶瓷热导率仅为20W/(m·K)左右。通过优化比例与烧结工艺,目前其热导率已达106W/(m·K)。Si3N4的热膨胀系数约为3.0×10-6/℃,与Si、SiC和GaAs等材料匹配良好,这使Si3N4陶瓷成为一种极具吸引力的高导热电子器件陶瓷基板材料。 现有陶瓷基板中,Si3N4陶瓷基板以其硬度高、机械强度高、耐高温和热稳定性好、介电常数和介质损耗低、耐磨损、耐腐蚀等优异的性能,被认为是综合性能最好的陶瓷材料。目前在IGBT模块封装中得到青睐,并逐步替代Al2O3和AlN陶瓷基板。
五、碳化硅(SiC)
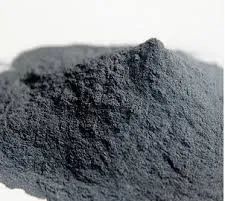
单晶SiC以第三代半导体材料而被大家熟知,其具有禁带宽度大、击穿电压高、热导率高以及电子饱和速度高等优点。
通过在SiC中添加少量的BeO和B2O3来增加其电阻率,再添加相应的烧结助剂在1900℃以上的温度中使用热压烧结,即可制备出致密度达98%以上的SiC陶瓷。采用不同的烧结方法、烧结助剂制备出的不同纯度的SiC陶瓷,其室温下热导率为100~490W/(m·K)。由于SiC陶瓷的介电常数非常大,因而其只适合低频应用,并不适合高频应用。
目前, 国内常用陶瓷基板材料主要为Al2O3、AlN和Si3N4。LTCC技术制作的陶瓷基板可在三维结构中集成电阻、电容和电感等无源元件。相对于半导体主要是有源器件的集成,LTCC拥有高密度的三维互连布线功能。
参考文献:
1、陆琪,刘英坤,乔志壮等. 陶瓷基板研究现状及新进展;
2、刘雄章,郭冉,李青达等.高热导率氮化硅散热基板材料的研究进展;
3、刘佳佳,刘英坤,谭永亮.SiC 电力电子器件研究现状及新进展;
4、郑锐,席生岐,周敬恩.AlN 低温烧结助剂的研究现状。